Hardox wear plate - strength and durability for industrial applications
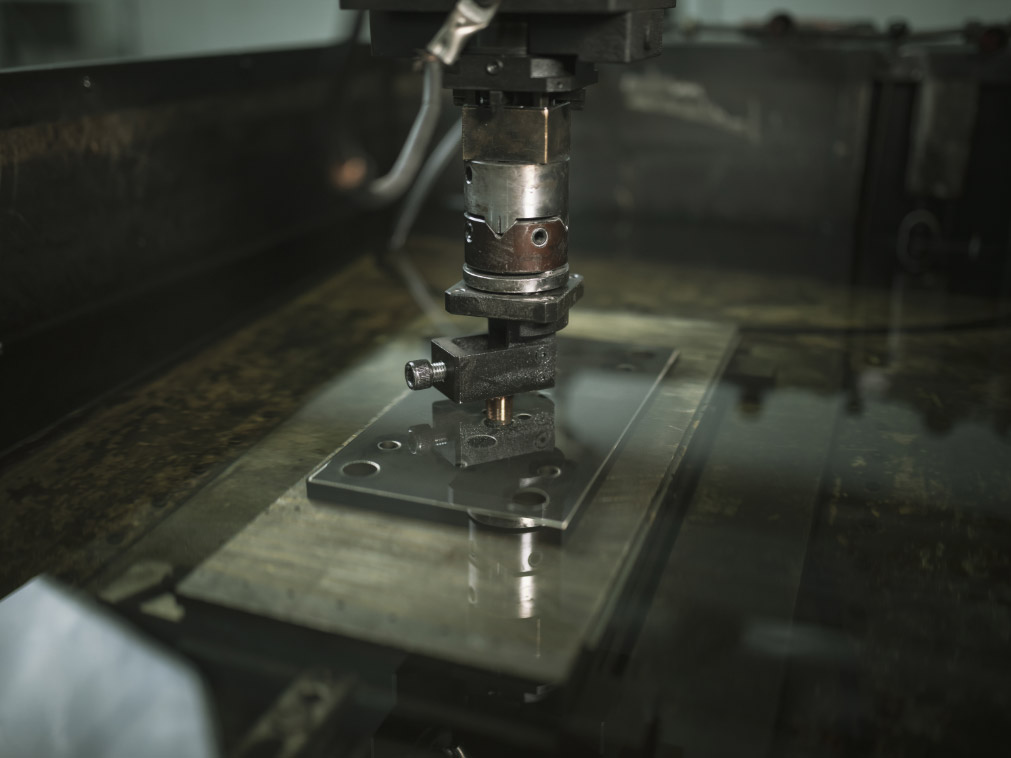
Hardox wear plate is a wear-resistant steel solution manufactured by the Swedish company SSAB. It is designed to withstand extreme conditions and offers a unique combination of hardness, toughness, and impact resistance, making it ideal for various industrial applications. This article will explore what a Hardox wear plate is, the types available, its distinctive features, and its multiple applications.
What is Hardox wear plate?
Hardox is a registered trademark of SSAB that encompasses a range of high-strength steel products, including wear plates. Hardox wear plates are made primarily from low-alloy carbon steel, which is heat-hardened to provide exceptional wear and abrasion resistance.
Types of Hardox wear plates
Hardox 400: This variant offers a nominal hardness of 400 HBW (Brinell Hardness). It is suitable for applications requiring moderate wear resistance under impact conditions.
Hardox 450: With a higher hardness of approximately 450 HBW, this sheet is suitable for applications that experience severe abrasive wear.
Hardox 500: This material offers a hardness of approximately 500 HBW and exceptional wear resistance, making it ideal for environments with extreme abrasive conditions.
Hardox 600: This type is the toughest, with a hardness of up to 600 HBW. It is suitable for extreme applications requiring exceptional wear and abrasion resistance.
Distinctive features of Hardox
High hardness: All Hardox variants offer exceptional hardness, making them highly resistant to wear and abrasion.
Good toughness: Despite its high hardness, Hardox sheet also exhibits good toughness, making it resistant to cracking and fracture under impact loads.
Low weight: Hardox is relatively light despite its strength compared to other materials, such as manganese steel, making it easy to handle and install.
Weldability: The hardox wear plate is readily welded using conventional welding techniques, allowing it to be adapted to various designs and applications.
IAM Group, EDM cutting of Hardox wear plate
Due to their high strength and hardness, specialised cutting methods are required to cut Hardox wear plates. One of the most effective methods for cutting this sheet is EDM cutting. This process uses controlled electrical discharges to erode the material and create the desired cut. In the case of Hardox sheets, EDM cutting allows for precise, clean cuts without significantly affecting the material's structural integrity. This method is beneficial when complex shapes need to be cut or when working with high-hardness materials such as Hardox.
Another method is high-pressure waterjet cutting, which is similar to EDM cutting. Each method has advantages and is selected according to project specifications, equipment availability, and required accuracy. Either way, proper tools, equipment, and recommended safety practices are essential to ensure accurate and safe cuts in Hardox sheet metal.
Grupo IAM has seven wire EDM machines, two penetration EDM machines, one drilling EDM machine for holes from Ø0.3 to Ø3 mm and a three-dimensional measuring machine. This way, Grupo IAM can provide its clients with a high-quality cut thanks to experience and state-of-the-art production means.