Die sink EDM for inconel valve caps
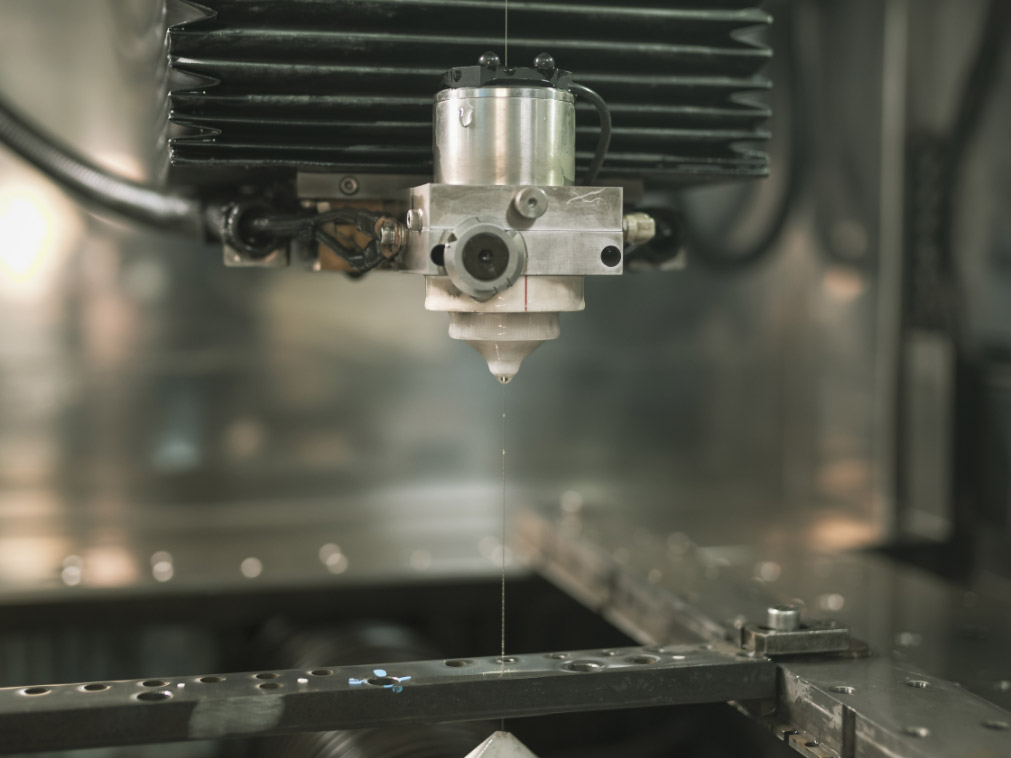
Die sinkEDM allows the creation of components with different surface layers. It is also helpful in machining fragile elements and achieving complex geometries and fine surface finishes.
In this real example carried out by Grupo IAM, we explore how IAM made its Die sinking EDM process available to a company in the valve sector to produce high-quality valve caps in a demanding material such as Inconel, a nickel-chromium alloy known for its resistance to high temperatures and corrosion.
Electroerosion for the Valve Sector
The manufacturing process for Inconel valve caps presented a challenge due to the material's extreme hardness. The final adjustment in such a hard material is minimal, requiring a meticulous approach at each step of the process. Additionally, the complexity of controlling various operations adds extra difficulty.
Grupo IAM's process began with the raw material, a bar or round Inconel. From there, a cutting operation was performed to obtain the piece's thread in its initial round shape. This rounded shape, inside and outside the valve cap, is achieved using die-sinking EDM.
In the main phase of the process, Die-sinking EDM is carried out using advanced equipment such as the Charmilles 440, a machine renowned for its precision and ability to work with high-hardness materials. Finally, the machining process is completed in a machining centre to ensure the final product's precision and quality.
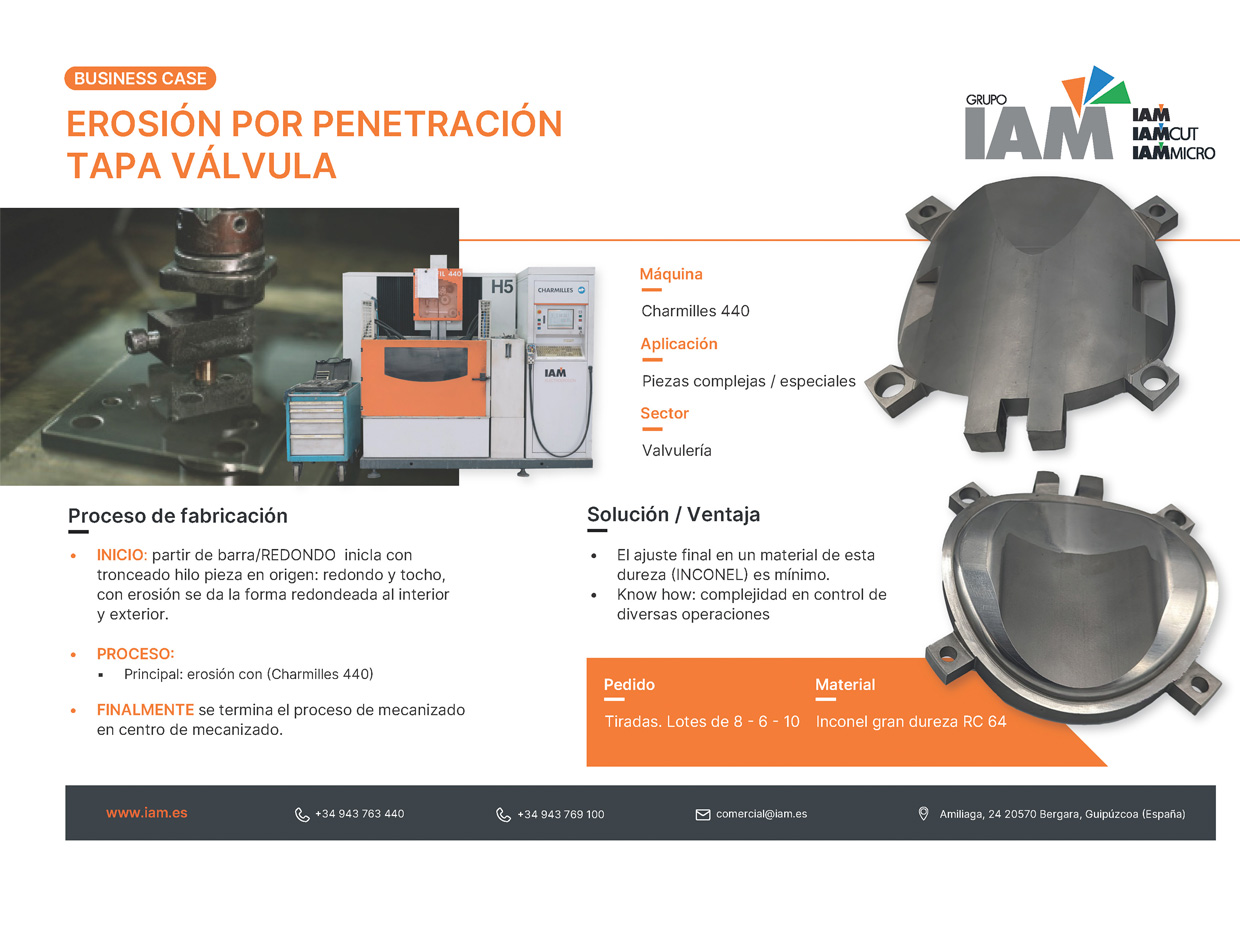
Production of Complex Parts in Batches
The Die sinking EDM process provides Grupo IAM with significant advantages, such as producing complex parts with exceptional precision, as demonstrated in this successful case with valve caps, even in challenging materials like Inconel.
This project by Grupo IAM demonstrates how electroerosion is suitable in manufacturing processes with exceptionally demanding materials. The combination of advanced technology, such as Die sinking EDM, with in-depth knowledge of the material and process needs provided by IAM, has been vital in supplying the required number of valve caps in batches of 8, 6, and 10, as the customer demands.
Grupo IAM, Advanced Manufacturing
Grupo IAM stands out in electric motor component manufacturing by implementing wire electroerosion. This approach highlights the importance of seeking complex solutions and adopting advanced technologies in the industry. Additionally, it emphasises their ability to select suitable materials and manage them efficiently. These improvements have elevated production quality and efficiency and established Grupo IAM as a prominent choice for producing dies, moulds, and particular parts in various industrial sectors.
With its numerous advantages, wire electroerosion is recognised as a valuable tool in this process. Please contact us to learn more about Grupo IAM or the different high-precision cutting methods.